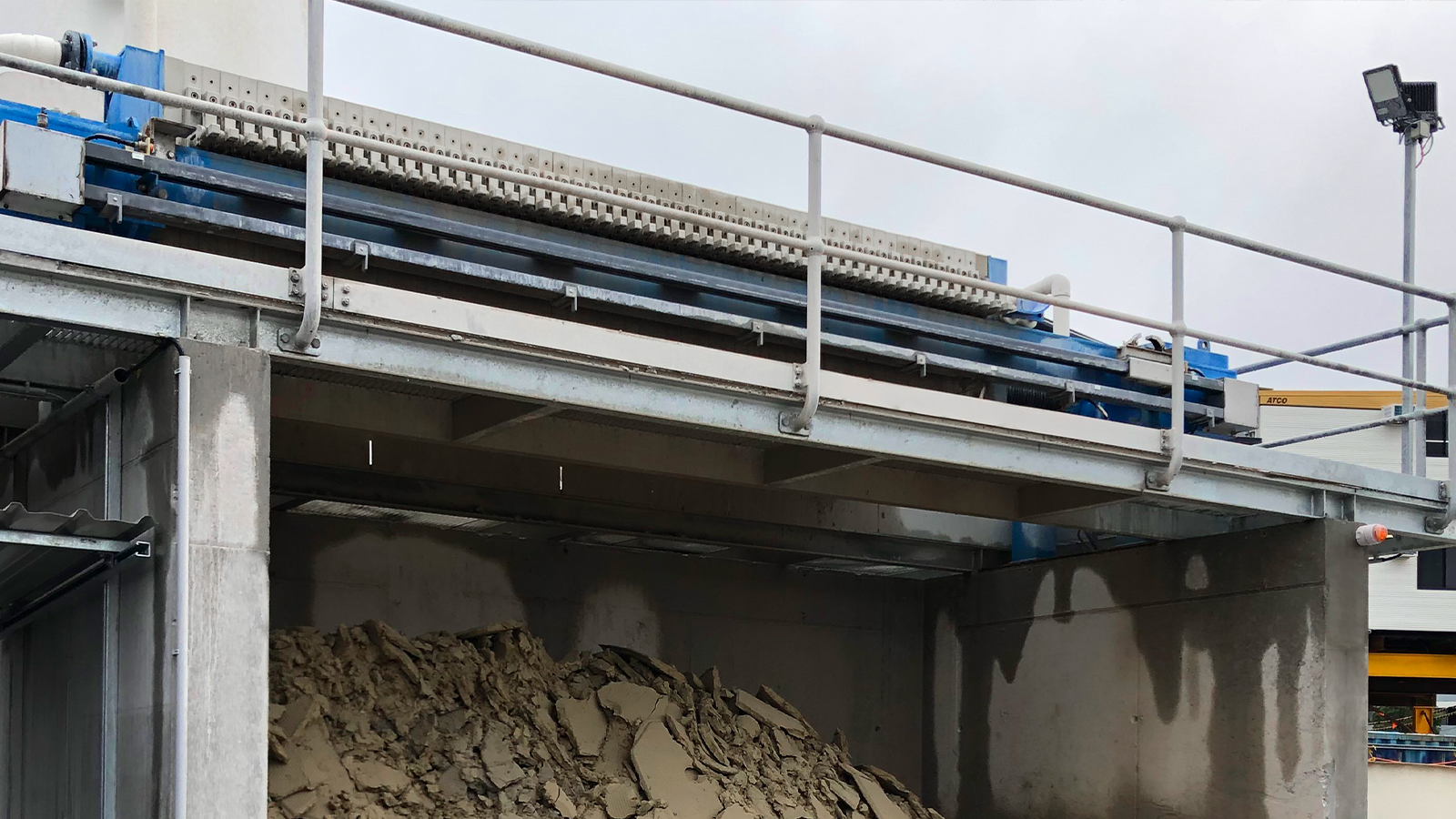
CakeMax® Filter Press
Hydroflux is proud to be Australia’s first water treatment and technology company to achieve Climate Active carbon neutral certification for our entire organization. As part of our climate change mission, we continue to research, develop and invest in sustainable technologies.
Now our journey continues – our main range of water technology and associated chemical products are Climate Active certified as carbon neutral. To read more on our journey, click HERE

The Hydroflux chamber filter press is a batch dewatering system and is ideally suited to small to medium volumes of sludge.

A filter press can offer several advantages over other dewatering systems:
- Very dry filter cake up to 60% dry solids
- Operational requirements are very low
- Capital cost is low
- Minimal chemistry if any is required
- Maintenance is relatively simple and can usually be undertaken by a non- specialised maintenance team
- Start up and shut down is quick and simple
Find out more
General filter press operational concept
A filter press comprises a series of interconnected plates fitted with filter cloths held together by a hydraulic ram. The plates are designed so that there is a void in between each plate where dewatering of the slurry occurs based on the pressure applied by the feed pump.

The photographs above show an automated filter press operating at a construction site in NSW. In the left photograph, the filter press is closed and in it filling and dewatering cycle. Once the dewatering cycle is complete, the press opens allowing the dewatered cake to drop into a storage bin below (right)
Filter press dewatering process
The first stage of dewatering in a filter press is chemical conditioning. This is usually achieved by dosing a polymer into a mixed sludge storage tank upstream of the filter press. The flocculant will bind the sludge particles into larger flocs which are larger and easier to dewater in the press.
The stages of dewatering in a filter press are as follows (please see diagram below):
- The chamber is empty and has been sealed closed by the hydraulic ram. The press is ready to receive wet solids.
- The wet solids are fed into the chamber and the solids begin to fill the chamber void.
- As the pressure builds up, the water is filtered through the filter cloths to drain.
- When the pressure reaches a set value, the dewatering cycle ends, and the feed stops.
- The hydraulic ram is retracted and the plates are released manually or automatically. This allows the cake solids to fall from between the plates into a bin or conveyor below.

The photograph above shows an automated filter press dewatering solids removed in a clarifier treating wastewater and ground water at a construction site. The design in this case involved elevating the press on a platform and allowing the sludge drops into a bunker below for disposal.
Filter press capacities
The Hydroflux Filter Presses are available with various plate sizes, numbers of plates, and automation.
The capacity of the filter press is defined as the volume of dewatered cake that will be generated for each batch which depends on the size of the plate, the number of plates installed, and the duration of the filtration cycle.
The following table provides indicative capacities of filter presses as defined as the cake volume when using various size plates. The daily capacity depends on the dewatering cycle time which will vary subject to the application and can range from 4-24 cycles per day or more.
Sizing Table
Plate Size | Cake Volume Litres – Chamber Plates | Cake Volume Litres – Membrane Plates |
470mm square | 25-150 | – |
500mm square | 40-170 | – |
630mm square | 100-410 | 110-460 |
800mm square | 350-850 | 500-1200 |
1000mm square | 760-1550 | 750-1850 |
1200mm square | 1020-2400 | 1600-3700 |
1300mm square | 1300-3400 | 1900-4900 |
1500mm square | 1800-4700 | 2500-8500 |
More sizes are available, please contact Hydroflux for sizing for your application.
Automation
Filter presses can be semi-automatic or fully automated. Semi-automatic filter presses rely on an operator to release the hydraulic ram once the dewatering cycle is complete. Once the pressure is released, each of the plates are pulled apart allowing the filter cake to drop into a bin below.
The fully automated filter press uses a pneumatic plate shifter to automatically open the plates once the press has completed the dewatering cycle. Automation of the filter press considerably increases the daily capacity of the unit by increasing the number of cycles that can be completed without operator intervention.

The photographs above show the automatic plate shifting mechanism of a fully automated filter press operating at a construction site.
The nature of the filter press dewatering process makes the filter press most suited to non-greasy applications such as the metal processing and construction industry where dry solids concentrations in excess of 60% are possible however Hydroflux has successfully used filter presses in many other applications including:
- Metal Processing
- Ground Water Treatment
- Site Remediation
- Breweries & Wineries
- General Industry
- Heavy Industry
- Pulp & Paper
- Vegetable Industry
A small filter press as part of a small industrial wastewater treatment plant in NSW
Hydroflux employs qualified civil, mechanical, chemical and electrical engineers plus a team of experienced project managers, site supervisors, commissioning engineers and service technicians based in offices in most capital cities providing a local presence throughout the duration of the project.
All projects are conducted under externally approved occupational health and safety, and environmental management systems.
Hydroflux is Australia’s first Water-tech company to achieve Climate Active certifications which means his means you are engaging with a carbon neutral organisation without increasing your carbon footprint and you are supporting positive and verified action on climate change.

Construction of a turnkey wastewater treatment plant at a new food production facility in SA.
Hydroflux can complete all the following works in-house which are typically required to construct a wastewater treatment plant.
- Process design, development of PID’s and HAZOPS reviews
- Establishment of the most suitable wastewater treatment plant layout
- Equipment and component selection
- Civil and building designs including preparation of documentation for council or other regulators
- Electrical design and programming
- Project management and site supervision
- Environmental / Occupational health and safety plans and report
- Quality assurance plans
- Earthworks, civil works, building works, mechanical and electrical installation
- Commissioning, training and documentation as required.

Stainless steel panel tanks are often used for aeration tanks.